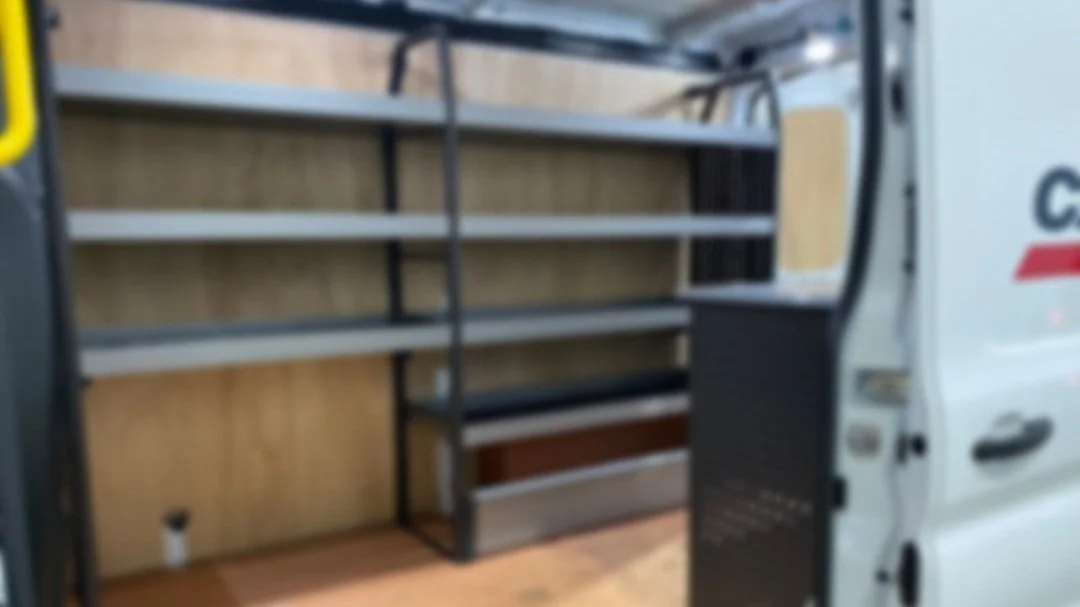
Homemade racking meant Haynes Agricultural’s mobile technician team had untidy, unprofessional-looking vans, which were taken off the road for a week at a time while the technicians built and installed their racking.
Whitebox were appointed to design and install van racking in each of the 50 mobile technician’s vans. With a consistent design across the fleet, Whitebox continues to work closely with Alan Thompson and his team to order and install the racking on site.
Results
Tidy, professional-looking vans across the fleet
Consistent layout means technicians can easily switch between vans without affecting their productivity
It now takes half a day for technicians to get set up in a new van, rather than taking a week to build their own racking
Untidy, unprofessional, disorganised vans
When Group Service Manager, Alan Thompson joined the business in 2019, his first job was to change the appearance of the vans and make them more professional.
His issue was how untidy the vans were. The technicians live and work out the back of their vans and their customers see them every day. But none of them were the same. Every bit of racking was handmade from bits of steel, and they looked untidy and unprofessional.
Plus, there was a lot of time wasted when technicians swapped vans or when new technicians joined the business.
“It was taking them a week. They were building it on work time and then putting it in. It didn’t look good at all”
Van racking designs and processes developed for the mobile technician team
After a bit of research, Alan got in touch with Whitebox to discuss the van racking solutions they had on offer. They met at Hayne’s depot in Kent and talked through the issues and the possible solutions.
Mark’s first role out of college was a mobile agricultural technician, so he quickly understood the challenge and was able to come up with designs that would meet the needs of the team at Haynes.
Once they’d created a solution that worked for Alan’s team, they developed a process that was quick and efficient, and minimised the amount of time each van was off the road.
As an approved installer, Mark places orders with System Edström, which are then delivered directly to the appropriate Haynes branch. Once the delivery arrives, Mark and his team travel to each branch to install the van racking.
The process is quick, clean and efficient. Whitebox keeps Alan informed about delivery times and locations, then arranges installation to suit their schedule. If something goes wrong, Whitebox sorts it directly with the manufacturer.
As vans are replaced, the racking is moved from the old van into the new one, saving time and money for Haynes. In fact, the process is so quick and simple, the technicians can do it themselves
“It’s quick. It really is.
Mark can get two done in a day, which means the vans are fitted out and ready to go.”
Professional, neat and tidy van racking that keeps everything safe and organised
With a standardised solution across the fleet, the look and layout of all the vans is exactly the same.
This presents a consistent, professional look to the customer and means the technicians know where everything is, whatever van they use.
Whereas before, the vans were disorganised and untidy, now the technicians have drawers and shelves to keep their tools and equipment organised and safe.
Plus, when it comes to swapping vans, the engineers simply empty their tools and equipment from one van and put them in the same places in the new one. Rather than losing a week each time, now it only takes half a day.
“It looks professional, and each van is exactly the same the way it’s laid out. It keeps everything uniform and clean. It keeps everything neat and tidy.”
Company details
With origins tracing back to 1790, Haynes Group is one of the oldest businesses still going in the UK. It is family owned, with CEO Andrew Haynes the sixth generation of the Haynes family to run the company.
Haynes Agricultural operates out of seven depots, located in Wrotham, Great Chart, Uckfield, Birchington, Horsham, Newbury and Winchester. They’re the main dealers for JCB and New Holland, and distributors for most leading farm machinery manufacturers.
Alan Thompson is the Group Service Manager for Haynes Agricultural, overseeing operations, sales growth and client relationships.
He manages 4 managers who then are responsible for their mobile technician team, with approximately 50 vans, each racked out with System Edström van racking, including a workbench and storage for tools and equipment.